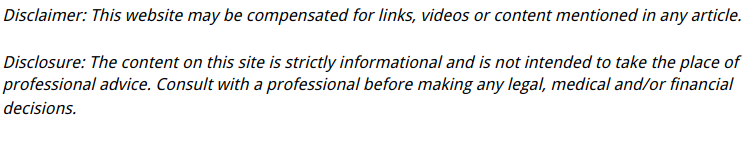
Because of their many uses, air compressors must stay in top condition to work properly. This tool is used to keep your home improvement, agricultural endeavors, and more applications of these helpful components running smoothly. If you own a home or operate a business, you’re more likely than not to have some tool or piece of equipment that won’t function properly without compressed air. When your air compressor is having issues, you have to be able to spot the warning signs that this part of your tools or machinery is in trouble before you can explore compressed air solutions.
Even the most efficient air compressor or air compressor system isn’t immune to having problems. Some air compressors may be easier to notice when they aren’t making air compressed in the way they once did than others, so getting to know how your model functions is what matters more than anything in this situation. From filling flat tires to powering machines to do heavy lifting to giving spray guns the ability to perform their functions, air compressors do a surprising amount of work for us. If we treat them right and fix issues as soon as we notice them, air compressors will make our work easier.

We rely upon our utilities for our daily needs. Everything from cooking to the laundry to even high-level manufacturing is dependent in one way or another on utilities. Some utilities we’re fairly familiar with. The main three are electricity, natural gas, and water. We see them on a regular basis on our utility bills, and we hear about them all the time in the news — in part because some of them are based on non-renewable resources. But the fourth most commonly-used utility, compressed air, is not as widely discussed. Many people don’t even understand how compressed air works if it is one of their utilities. If it isn’t, they don’t know whether or not it’s something they can take advantage of. Below, we’re going to look into air compressor piping. The more you understand how air compressor piping works, the better you’ll be able to be responsible about your use of this fourth utility. Furthermore, you’ll be less likely to have interruptions in your use of this utility. You’ll know when to call professionals for help, and how to maintain the piping that you’ve possibly already become dependent on.
Air Compressor Piping: The Basics
Whether or not you’re aware of the ins and outs of compressed air, it’s an undisputed fact that about 70% of all manufacturers have a compressed air system. Certainly, manufacturers are particularly familiar with air compressor piping. It keys into how the system operates as a whole, with some compressed air piping designs being more suited to manufacturing needs than others. Plenty of things go into choosing one compressed air system over another — from compressed air piping sizing to compressed air piping layouts. Some forms of piping aren’t even made of the same materials as others. Certainly, you may find a difference in costs of one type of material versus another. While air compressor systems at their best are great utilities, when they don’t work as they should manufacturers risk losing a good deal of money. It’s important, therefore, for manufacturers to be aware not only of how these systems work, but what happens when they go wrong.
When Air Compressor Systems Go Wrong: What To Be Aware Of
One of the main issues that can occur with compressed air systems is that of system leaks. These usually occur when there is a hole in the piping, and even a small hole can be extremely costly. A hole that’s just 1/8 inch in diameter in a 100 psi system can cost someone over $1,200 per year in wasted energy. While some manufacturers in particular may balk at the idea of spending extra time and money on air compressor piping maintenance, it’s certainly less expensive to maintain piping compared to the costs of one or several holes in the piping. Another issue that can occur is a drop in pressure. In a well-designed system, pressure loss isn’t much of a concern. In fact, it’s less than 10% of the compressor’s discharge pressure — which can be found on a gage on the outlet of the compressor. But if the pressure loss is over 10%, your distribution system needs to be evaluated to identify the area or areas involved in significant pressure drops. For every two pounds per square inch drop in pressure will reduce operating costs by 1.5%.
Heat And Compressed Air: The Conversion
What happens to the electrical energy used by compressed air systems? Much of the time, it’s converted to heat. In fact, 80 to 90% of the electrical energy used by an air compressor is now converted to usable heat. This heat isn’t necessarily always recovered, but it can be recovered. This requires the use of a heat recovery unit. With a properly designed heat recovery unit, 50% to 90% of recovered heat can be used for heating and water. This creates a system that can be used in multiple ways, ultimately saving the manufacturer money.